The one place all petrolheads should check out when in Spartanburg
03 Jul 2018|8,444 views
Spartanburg? Isn't that where Gerard Butler kicked the butts of, like, a million Persians? No, that was Sparta in the 300 movie. This is a city in South Carolina, U.S.A.
When we think of the U.S.A, cities like New York, Las Vegas and Los Angeles (to name a few) usually come to mind. What most of us are unaware of is the existence of the lesser-known city called Spartanburg. So what's so special about this place? You may ask.
Formed in 1785, and named after a local militia called the Spartan Regiment in the American Revolutionary War, Spartanburg boasts a rich history, beautiful landscapes and super-friendly locals. Oh, and did we mention that it is also the home of the new BMW X4?
X marks the spot for Spartanburg
Launched over 25 years ago, the BMW Group Plant Spartanburg is responsible for the production of the X3, X4, X5, X6, as well as the upcoming X7. It has produced over four million vehicles since it opened, has a maximum production capacity of 450,000 units, and exports 70% of those units to over 140 markets around the world.
Modelled after the BMW plant in Lyserg, Germany, the American plant spans 1,150 acres of land and employs over 10,000 associates with an amazingly low 3% employee turnover rate. Each associate is proficient in anywhere between four and six different jobs, which range from interior fitting to wheel alignment and 'dyno' testing.
To facilitate this, as well as maximise productivity, the plant also utilises German-made Kuka (one of the world's leading suppliers of robotics) robots. It even has an appropriately named cafe called The Kidney Grille.
Everything comes together like clockwork
With all parts manufactured and ready to go, all that's left to do is put it all together - a process, which takes a mere 32 hours from start to finish.
To put things into perspective, our journey from Singapore to Spartanburg took just a few hours short of that. To ensure everything runs smoothly, every computer within the assembly area is linked by approximately 26,000km of communications cables while specific jobs are split into smaller assembly lines called 'fingers'.
This attention to detail also carries over into ensuring employees are always at the most ergonomically-friendly position while working, by using machines to position the cars so that the associates don't develop back problems.
Assembling the X Force
Before it starts on the assembly line, every vehicle's bonnet is affixed with a transponder, which helps track the car throughout the entire process. It also comes with a Build Sheet, which helps associates identify which parts are to be installed on the car.
The car body - once formed, painted and protected - waits in the stacker at the start of the assembly line. Once called upon, its doors are removed and travel via an overhead conveyor to a separate door assembly line - where the glass, water seals, mirrors, airbags, speakers and other trim pieces are installed. They are then reunited with the same car body on the main line.
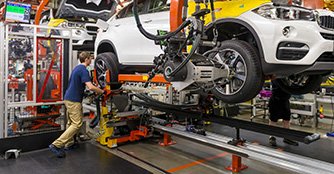

The Wiring Harness is then fastened throughout the cabin, boot and engine bay with the help of clips and wire ties.
The vehicle's powertrain is put together in a separate assembly area, where the engine, transmission, front/rear axles and other parts are assembled.
Once completed, the powertrain is moved via a floor transport system to the Marriage area, where the upper body of the car and powertrain come together for the first time. It is also the first time the vehicle touches the ground with its tyres.
Next comes the fluids. Almost all fluids - including radiator, brake, power steering, coolant, and fuel - are added to the car at this point. Employees also use a special gas, which has additional cleaning agents and lubricants, to help with the car's first ever start up.
This is followed by head light and wheel alignment, as well as a 'dyno' test, which allows the car to be driven at speeds of up to 150km/h and allows for a proper testing of the powertrain.
At the final inspection area, associates scrutinise every part of the interior and exterior to make sure everything is in order before the car is driven off the line and onto an indoor driving track, where the xDrive and ABS systems are tested.
If nothing stands out, the car is then driven back inside for a final fit and finish, where the iconic BMW roundel is installed using a rubber mallet. They call this 'spanking the baby'.
The final station of the assembly line ensures the vehicle is free of scratches on delivery with the installation of protective sheets and foams. Once all that is done, the car goes out a final set of blue shutters - the point of no return.
The Yanks don't make crap cars no more
With German carmakers such as BMW, Mercedes-Benz and Volkswagen opening manufacturing plants in the U.S.A, does the stereotype that Americans make less-than-ideal driving machines still hold true? Maybe not. Well, technically they are still German, but you know what I mean.
The bottom line is, the next time you're planning a trip to the States, be sure to include a detour to Spartanburg and check out the BMW Group Plant. You won't regret it.
Spartanburg? Isn't that where Gerard Butler kicked the butts of, like, a million Persians? No, that was Sparta in the 300 movie. This is a city in South Carolina, U.S.A.
When we think of the U.S.A, cities like New York, Las Vegas and Los Angeles (to name a few) usually come to mind. What most of us are unaware of is the existence of the lesser-known city called Spartanburg. So what's so special about this place? You may ask.
Formed in 1785, and named after a local militia called the Spartan Regiment in the American Revolutionary War, Spartanburg boasts a rich history, beautiful landscapes and super-friendly locals. Oh, and did we mention that it is also the home of the new BMW X4?
X marks the spot for Spartanburg
Launched over 25 years ago, the BMW Group Plant Spartanburg is responsible for the production of the X3, X4, X5, X6, as well as the upcoming X7. It has produced over four million vehicles since it opened, has a maximum production capacity of 450,000 units, and exports 70% of those units to over 140 markets around the world.
Modelled after the BMW plant in Lyserg, Germany, the American plant spans 1,150 acres of land and employs over 10,000 associates with an amazingly low 3% employee turnover rate. Each associate is proficient in anywhere between four and six different jobs, which range from interior fitting to wheel alignment and 'dyno' testing.
To facilitate this, as well as maximise productivity, the plant also utilises German-made Kuka (one of the world's leading suppliers of robotics) robots. It even has an appropriately named cafe called The Kidney Grille.
Everything comes together like clockwork
With all parts manufactured and ready to go, all that's left to do is put it all together - a process, which takes a mere 32 hours from start to finish.
To put things into perspective, our journey from Singapore to Spartanburg took just a few hours short of that. To ensure everything runs smoothly, every computer within the assembly area is linked by approximately 26,000km of communications cables while specific jobs are split into smaller assembly lines called 'fingers'.
This attention to detail also carries over into ensuring employees are always at the most ergonomically-friendly position while working, by using machines to position the cars so that the associates don't develop back problems.
Assembling the X Force
Before it starts on the assembly line, every vehicle's bonnet is affixed with a transponder, which helps track the car throughout the entire process. It also comes with a Build Sheet, which helps associates identify which parts are to be installed on the car.
The car body - once formed, painted and protected - waits in the stacker at the start of the assembly line. Once called upon, its doors are removed and travel via an overhead conveyor to a separate door assembly line - where the glass, water seals, mirrors, airbags, speakers and other trim pieces are installed. They are then reunited with the same car body on the main line.
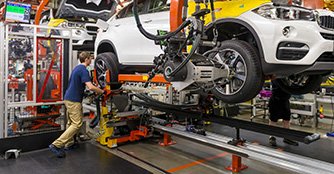

The Wiring Harness is then fastened throughout the cabin, boot and engine bay with the help of clips and wire ties.
The vehicle's powertrain is put together in a separate assembly area, where the engine, transmission, front/rear axles and other parts are assembled.
Once completed, the powertrain is moved via a floor transport system to the Marriage area, where the upper body of the car and powertrain come together for the first time. It is also the first time the vehicle touches the ground with its tyres.
Next comes the fluids. Almost all fluids - including radiator, brake, power steering, coolant, and fuel - are added to the car at this point. Employees also use a special gas, which has additional cleaning agents and lubricants, to help with the car's first ever start up.
This is followed by head light and wheel alignment, as well as a 'dyno' test, which allows the car to be driven at speeds of up to 150km/h and allows for a proper testing of the powertrain.
At the final inspection area, associates scrutinise every part of the interior and exterior to make sure everything is in order before the car is driven off the line and onto an indoor driving track, where the xDrive and ABS systems are tested.
If nothing stands out, the car is then driven back inside for a final fit and finish, where the iconic BMW roundel is installed using a rubber mallet. They call this 'spanking the baby'.
The final station of the assembly line ensures the vehicle is free of scratches on delivery with the installation of protective sheets and foams. Once all that is done, the car goes out a final set of blue shutters - the point of no return.
The Yanks don't make crap cars no more
With German carmakers such as BMW, Mercedes-Benz and Volkswagen opening manufacturing plants in the U.S.A, does the stereotype that Americans make less-than-ideal driving machines still hold true? Maybe not. Well, technically they are still German, but you know what I mean.
The bottom line is, the next time you're planning a trip to the States, be sure to include a detour to Spartanburg and check out the BMW Group Plant. You won't regret it.
Thank You For Your Subscription.