Electric mobility through specialisation for Volkswagen plants
14 Jul 2019|2,994 views
With pre-series production of the Volkswagen ID.3 beginning at their plant in Zwickau, the firm is adopting a high-specialisation model to build its all new electric vehicles, by delegating the production of other various core components throughout the Volkswagen Group components plants. For the ID.3, the electric drive will come from Kassel, while the Salzgitter plant will supply its colleagues in Hessen with rotors and stators. The Brunswick plant meanwhile will develop and produce the battery system, with other sites responsible for delivering castings and other parts.
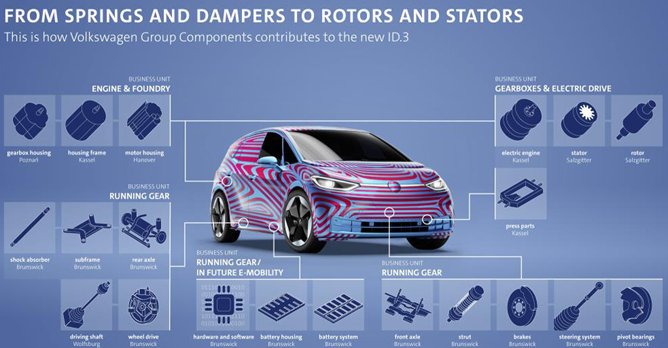

The Group Components plant in Kassel supplies electric drives and platform parts for the ID.3. In addition to the dual-clutch gearbox, the plant will chiefly be producing electric drives for the Modular Electric Drive Matrix (MEB). All parts for the electric drive are put together at the Kassel plant, including the parts from the component plants in Salzgitter, Poznan, and Hanover.
Kassel will produce electric drives for all MEB vehicles in Europe and North America. Production of pre-series drives has already started; and in the future, up to 500,000 units will leave the factory each year. Kassel works closely with the Chinese plant in Tianjin where the electric drive is produced in parallel for the Chinese market. Together, the two plants will produce up to 1.4 million electric drives each year from 2023 onwards. This means that Volkswagen Group Components will be one of the largest global manufacturers of electric vehicle drives in the future.
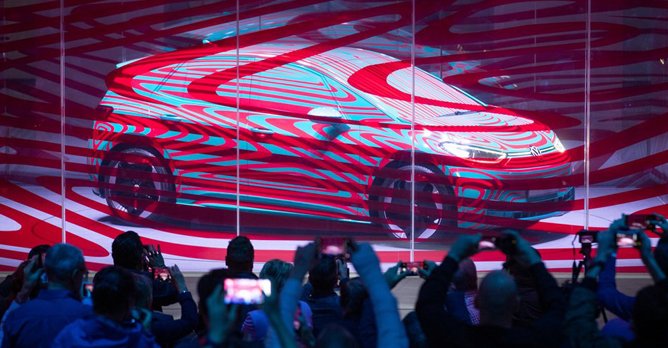

Volkswagen expects up to 2,000 rotors and stators will be produced each day, and in order to achieve these high volumes, a new hairpin technology will be used to manufacture stators, enabling improved performance figures in shorter production times.
Salzgitter also supports the transformation process at Group Components, with Volkswagen Group Components assuming end-to-end responsibility at Volkswagen AG for the battery, starting with research and ending with the recycling process. The Salzgitter site has taken on key elements of these processes, with battery expertise being developed at the Center of Excellence and a pilot plant for battery production will be opened by the end of the year. This will be followed by a pilot plant for recycling in 2020. Competence and industrial processes are to be developed at both pilot plants.
Finally, the battery system for the ID.3 will be manufactured at Brunswick. A new hall the size of nine football pitches will be built especially for manufacturing the battery system, scheduled to open in the fourth quarter of 2019. Volkswagen expects around 2,000 units will be produced per day and delivered to the vehicle production site in Zwickau. The Brunswick site has been steadily developing its battery expertise since 2013.
With pre-series production of the Volkswagen ID.3 beginning at their plant in Zwickau, the firm is adopting a high-specialisation model to build its all new electric vehicles, by delegating the production of other various core components throughout the Volkswagen Group components plants. For the ID.3, the electric drive will come from Kassel, while the Salzgitter plant will supply its colleagues in Hessen with rotors and stators. The Brunswick plant meanwhile will develop and produce the battery system, with other sites responsible for delivering castings and other parts.
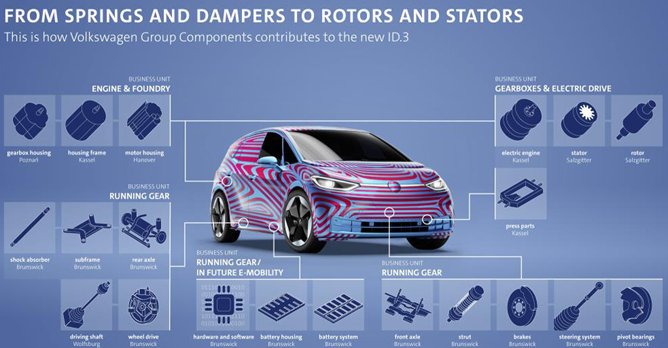

The Group Components plant in Kassel supplies electric drives and platform parts for the ID.3. In addition to the dual-clutch gearbox, the plant will chiefly be producing electric drives for the Modular Electric Drive Matrix (MEB). All parts for the electric drive are put together at the Kassel plant, including the parts from the component plants in Salzgitter, Poznan, and Hanover.
Kassel will produce electric drives for all MEB vehicles in Europe and North America. Production of pre-series drives has already started; and in the future, up to 500,000 units will leave the factory each year. Kassel works closely with the Chinese plant in Tianjin where the electric drive is produced in parallel for the Chinese market. Together, the two plants will produce up to 1.4 million electric drives each year from 2023 onwards. This means that Volkswagen Group Components will be one of the largest global manufacturers of electric vehicle drives in the future.
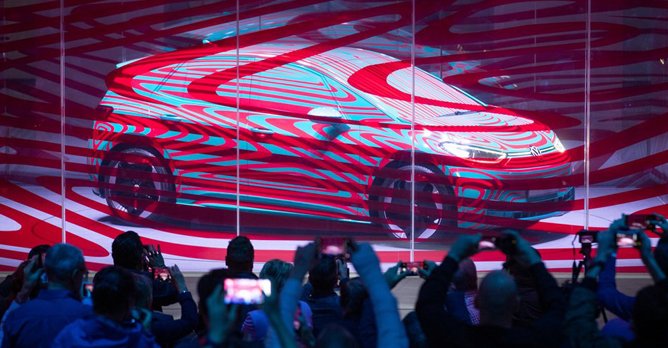

Volkswagen expects up to 2,000 rotors and stators will be produced each day, and in order to achieve these high volumes, a new hairpin technology will be used to manufacture stators, enabling improved performance figures in shorter production times.
Salzgitter also supports the transformation process at Group Components, with Volkswagen Group Components assuming end-to-end responsibility at Volkswagen AG for the battery, starting with research and ending with the recycling process. The Salzgitter site has taken on key elements of these processes, with battery expertise being developed at the Center of Excellence and a pilot plant for battery production will be opened by the end of the year. This will be followed by a pilot plant for recycling in 2020. Competence and industrial processes are to be developed at both pilot plants.
Finally, the battery system for the ID.3 will be manufactured at Brunswick. A new hall the size of nine football pitches will be built especially for manufacturing the battery system, scheduled to open in the fourth quarter of 2019. Volkswagen expects around 2,000 units will be produced per day and delivered to the vehicle production site in Zwickau. The Brunswick site has been steadily developing its battery expertise since 2013.
Latest COE Prices
May 2025 | 1st BIDDING
NEXT TENDER: 21 May 2025
CAT A$103,009
CAT B$119,890
CAT C$62,590
CAT E$118,889
View Full Results Thank You For Your Subscription.