Finally, Mercedes has started production of the Mercedes-AMG ONE
29 Aug 2022|1,241 views
Mercedes-AMG has started the production of the ONE hypercar for its customers after numerous delays that have plagued its production. Not surprisingly, Mercedes-AMG has claimed that the car is the most ambitious project they have ever undertaken from development to production.
The Mercedes-AMG ONE is completed by hand at a total of 16 assembly and testing stations. Some sub-systems are first pre-assembled and tested for function, then disassembled again and only then finally installed in the vehicle.
This applies, for example, to the carbon fibre monocoque with a bonded in roof as well as all detachable body parts, which are also made of the light and stable material. The entire outer skin is the first to be completely assembled.
Specialists then have to take into account the final lacquering, which adds its own material thickness. Given that the wall thickness of the carbon is only 1.2mm in certain locations, this makes it a highly specialised task.
Once everything fits together perfectly, parts including doors and bonnets are dismantled again and then hand painted as a car set for each individual vehicle. This is to ensure perfect colour matching of the entire vehicle.
Mercedes-AMG ONE's engine might only be 1.6 litres in displacement but is boosted by four powerful electric motors The next assembly step sees the marriage of powertrain and the body in white assembled together. The 1.6-litre V6 turbo engine, high-voltage battery and four electric motors have been previously hot tested to ensure they are healthy. This is exactly the same process as is done with Mercedes' Formula 1 Power Units.
In total, over 50 specialists work on each individual Mercedes‑AMG ONE. After each station, there are in-depth quality checks based on defined characteristics, resulting in extensive documentation of the production process.
The final stage of production is marked by a roll out at a nearby proving ground, where each Mercedes‑AMG ONE undergoes final acceptance testing by a factory test driver. The vehicle is then transported in a closed truck to the Mercedes‑AMG headquarters in Affalterbach where a technical briefing by experts and handover of the vehicle is done.
The Mercedes-AMG ONE is completed by hand at a total of 16 assembly and testing stations. Some sub-systems are first pre-assembled and tested for function, then disassembled again and only then finally installed in the vehicle.
This applies, for example, to the carbon fibre monocoque with a bonded in roof as well as all detachable body parts, which are also made of the light and stable material. The entire outer skin is the first to be completely assembled.
Specialists then have to take into account the final lacquering, which adds its own material thickness. Given that the wall thickness of the carbon is only 1.2mm in certain locations, this makes it a highly specialised task.
Once everything fits together perfectly, parts including doors and bonnets are dismantled again and then hand painted as a car set for each individual vehicle. This is to ensure perfect colour matching of the entire vehicle.
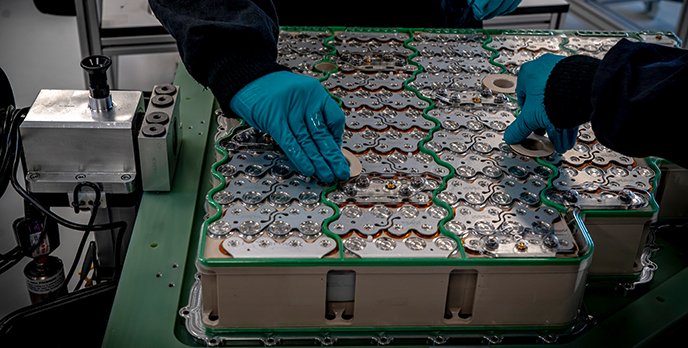

In total, over 50 specialists work on each individual Mercedes‑AMG ONE. After each station, there are in-depth quality checks based on defined characteristics, resulting in extensive documentation of the production process.
The final stage of production is marked by a roll out at a nearby proving ground, where each Mercedes‑AMG ONE undergoes final acceptance testing by a factory test driver. The vehicle is then transported in a closed truck to the Mercedes‑AMG headquarters in Affalterbach where a technical briefing by experts and handover of the vehicle is done.
Mercedes-AMG has started the production of the ONE hypercar for its customers after numerous delays that have plagued its production. Not surprisingly, Mercedes-AMG has claimed that the car is the most ambitious project they have ever undertaken from development to production.
The Mercedes-AMG ONE is completed by hand at a total of 16 assembly and testing stations. Some sub-systems are first pre-assembled and tested for function, then disassembled again and only then finally installed in the vehicle.
This applies, for example, to the carbon fibre monocoque with a bonded in roof as well as all detachable body parts, which are also made of the light and stable material. The entire outer skin is the first to be completely assembled.
Specialists then have to take into account the final lacquering, which adds its own material thickness. Given that the wall thickness of the carbon is only 1.2mm in certain locations, this makes it a highly specialised task.
Once everything fits together perfectly, parts including doors and bonnets are dismantled again and then hand painted as a car set for each individual vehicle. This is to ensure perfect colour matching of the entire vehicle.
Mercedes-AMG ONE's engine might only be 1.6 litres in displacement but is boosted by four powerful electric motors The next assembly step sees the marriage of powertrain and the body in white assembled together. The 1.6-litre V6 turbo engine, high-voltage battery and four electric motors have been previously hot tested to ensure they are healthy. This is exactly the same process as is done with Mercedes' Formula 1 Power Units.
In total, over 50 specialists work on each individual Mercedes‑AMG ONE. After each station, there are in-depth quality checks based on defined characteristics, resulting in extensive documentation of the production process.
The final stage of production is marked by a roll out at a nearby proving ground, where each Mercedes‑AMG ONE undergoes final acceptance testing by a factory test driver. The vehicle is then transported in a closed truck to the Mercedes‑AMG headquarters in Affalterbach where a technical briefing by experts and handover of the vehicle is done.
The Mercedes-AMG ONE is completed by hand at a total of 16 assembly and testing stations. Some sub-systems are first pre-assembled and tested for function, then disassembled again and only then finally installed in the vehicle.
This applies, for example, to the carbon fibre monocoque with a bonded in roof as well as all detachable body parts, which are also made of the light and stable material. The entire outer skin is the first to be completely assembled.
Specialists then have to take into account the final lacquering, which adds its own material thickness. Given that the wall thickness of the carbon is only 1.2mm in certain locations, this makes it a highly specialised task.
Once everything fits together perfectly, parts including doors and bonnets are dismantled again and then hand painted as a car set for each individual vehicle. This is to ensure perfect colour matching of the entire vehicle.
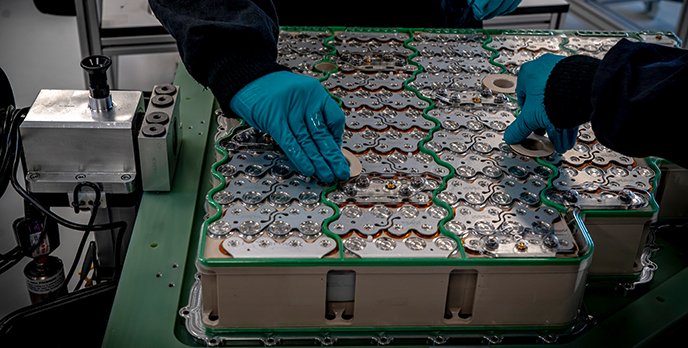

In total, over 50 specialists work on each individual Mercedes‑AMG ONE. After each station, there are in-depth quality checks based on defined characteristics, resulting in extensive documentation of the production process.
The final stage of production is marked by a roll out at a nearby proving ground, where each Mercedes‑AMG ONE undergoes final acceptance testing by a factory test driver. The vehicle is then transported in a closed truck to the Mercedes‑AMG headquarters in Affalterbach where a technical briefing by experts and handover of the vehicle is done.
Latest COE Prices
July 2025 | 2nd BIDDING
NEXT TENDER: 06 Aug 2025
CAT A$101,102
CAT B$119,101
CAT C$68,600
CAT E$120,000
View Full Results Thank You For Your Subscription.