Audi on the road toward CO2-neutral production sites
26 Nov 2020|689 views
Audi AG intends to contribute its share to achieving the Paris climate goals. The company has initiated a large number of actions along the entire value chain to support the vision of achieving carbon neutrality on the environmental balance sheet by 2050.
All actions to reduce the environmental footprint in manufacturing and logistics are concentrated in the environmental program billed as Mission:Zero. In addition to initial reports of success, there is a strategic plan for how the goal is to be achieved at the Audi locations by 2025, focused on one of the key challenges - a carbon-neutral automobile production footprint.
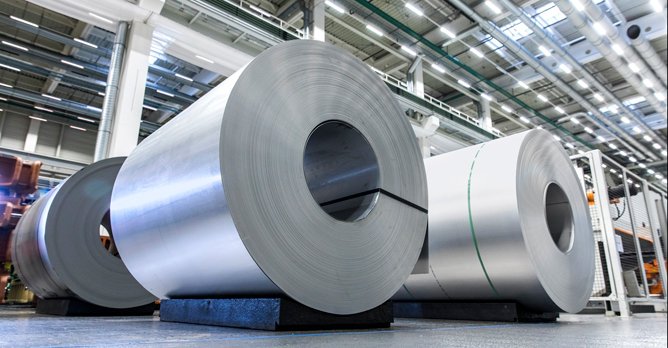

Audi produced about 1.8 million cars at its locations around the globe last year. Accordingly, making product manufacturing as sustainable as possible is an ambitious aspiration. Audi has set itself the ambitious goal of progressively achieving a 30% reduction of vehicle-specific CO2 emissions by 2025 - compared to the reference year of 2015 and along the entire product lifecycle.
The Gyor location, which recently became the second CO2-neutral Audi site, has been taking advantage of the geographic conditions since 2012 and covers around 70% of its heat requirement by geothermal energy, with the remaining 30% of required heat generated by natural gas, with its CO2 neutrality ensured by biogas certificates.
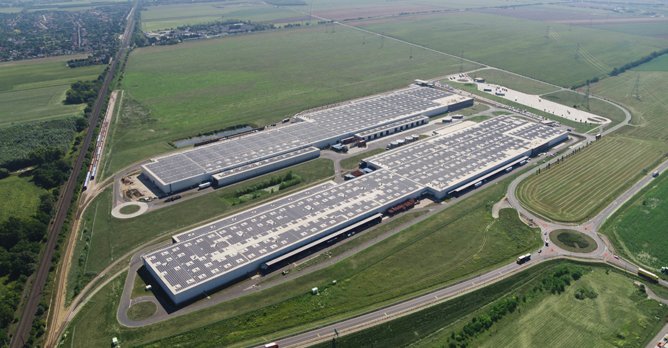

In 2012, the connection from Audi's Neckarsulm location to Emden was converted to 'green trains' as well. Since 2017, rail-bound logistics have been handled in a largely climate-neutral way with Deutsche Bahn. By switching to DB Cargo's 'DBeco plus' product, the company saves more than 13,000 metric tons of CO2 per year.
At the Ingolstadt site, two hybrid locomotives are used, and a rail-bound tractor with an electric motor plus a CNG (Compressed Natural Gas) volume tractor for shunting operations at the Neckarsulm location. Where rail-bound shipments are not possible, climate-friendly alternatives are used as well.
Due to the transition toward electric mobility, the proportion of CO2 emissions attributable to the supply chain increases because the battery production process in particular is CO2 intensive. At Audi, nearly a fourth of all CO2 emissions are anticipated to occur here by 2025, based on the forecast fleet average.
Therefore, Audi, together with its suppliers, is especially addressing actions that are effective in this early manufacturing stage.
With the rollout of the 'Aluminium Closed Loop' in Audi's stamping plants, the carbon footprint just in 2019 was reduced by 150,000 metric tons.
In collaboration with the Karlsruhe Institute for Technology (KIT), the two partners are working on a method for chemical recycling of automotive plastics. This method will make it possible to recycle mixed plastics. Going forward, this technology may become an eco-friendly alternative to mechanical recycling.
Another case in point for exemplary resource efficiency is the IN-Campus. In a joint venture with the city of Ingolstadt, Audi AG is rehabilitating the former complex of the Bayernoil refinery. With an area of 75 hectares, the IN-Campus is one of the largest rehabilitation projects in Germany. 15 hectares of the total area are intended to become a compensation area for nature. The project is planned to be completed by 2022.
Audi AG intends to contribute its share to achieving the Paris climate goals. The company has initiated a large number of actions along the entire value chain to support the vision of achieving carbon neutrality on the environmental balance sheet by 2050.
All actions to reduce the environmental footprint in manufacturing and logistics are concentrated in the environmental program billed as Mission:Zero. In addition to initial reports of success, there is a strategic plan for how the goal is to be achieved at the Audi locations by 2025, focused on one of the key challenges - a carbon-neutral automobile production footprint.
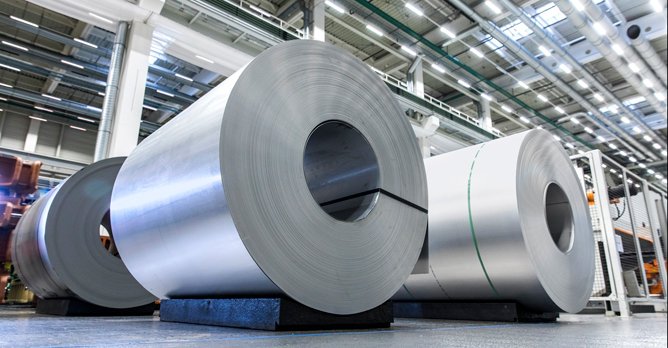

Audi produced about 1.8 million cars at its locations around the globe last year. Accordingly, making product manufacturing as sustainable as possible is an ambitious aspiration. Audi has set itself the ambitious goal of progressively achieving a 30% reduction of vehicle-specific CO2 emissions by 2025 - compared to the reference year of 2015 and along the entire product lifecycle.
The Gyor location, which recently became the second CO2-neutral Audi site, has been taking advantage of the geographic conditions since 2012 and covers around 70% of its heat requirement by geothermal energy, with the remaining 30% of required heat generated by natural gas, with its CO2 neutrality ensured by biogas certificates.
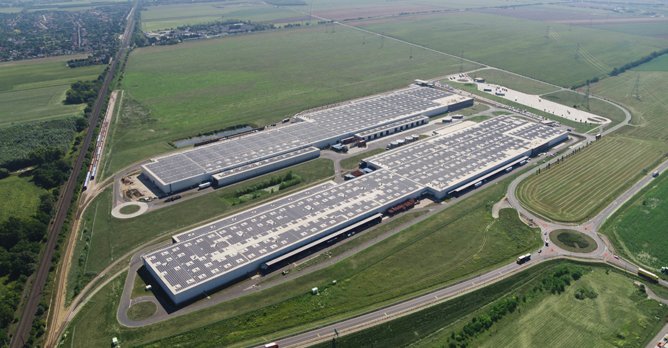

In 2012, the connection from Audi's Neckarsulm location to Emden was converted to 'green trains' as well. Since 2017, rail-bound logistics have been handled in a largely climate-neutral way with Deutsche Bahn. By switching to DB Cargo's 'DBeco plus' product, the company saves more than 13,000 metric tons of CO2 per year.
At the Ingolstadt site, two hybrid locomotives are used, and a rail-bound tractor with an electric motor plus a CNG (Compressed Natural Gas) volume tractor for shunting operations at the Neckarsulm location. Where rail-bound shipments are not possible, climate-friendly alternatives are used as well.
Due to the transition toward electric mobility, the proportion of CO2 emissions attributable to the supply chain increases because the battery production process in particular is CO2 intensive. At Audi, nearly a fourth of all CO2 emissions are anticipated to occur here by 2025, based on the forecast fleet average.
Therefore, Audi, together with its suppliers, is especially addressing actions that are effective in this early manufacturing stage.
With the rollout of the 'Aluminium Closed Loop' in Audi's stamping plants, the carbon footprint just in 2019 was reduced by 150,000 metric tons.
In collaboration with the Karlsruhe Institute for Technology (KIT), the two partners are working on a method for chemical recycling of automotive plastics. This method will make it possible to recycle mixed plastics. Going forward, this technology may become an eco-friendly alternative to mechanical recycling.
Another case in point for exemplary resource efficiency is the IN-Campus. In a joint venture with the city of Ingolstadt, Audi AG is rehabilitating the former complex of the Bayernoil refinery. With an area of 75 hectares, the IN-Campus is one of the largest rehabilitation projects in Germany. 15 hectares of the total area are intended to become a compensation area for nature. The project is planned to be completed by 2022.
Latest COE Prices
June 2025 | 2nd BIDDING
NEXT TENDER: 09 Jul 2025
CAT A$98,124
CAT B$116,670
CAT C$65,000
CAT E$116,889
View Full Results Thank You For Your Subscription.