Skoda sets production record at Kvasiny plant
18 Feb 2020|1,190 views
Skoda Auto has set a new record at the Kvasiny plant by building more than 320,000 vehicles at the site in 2019.
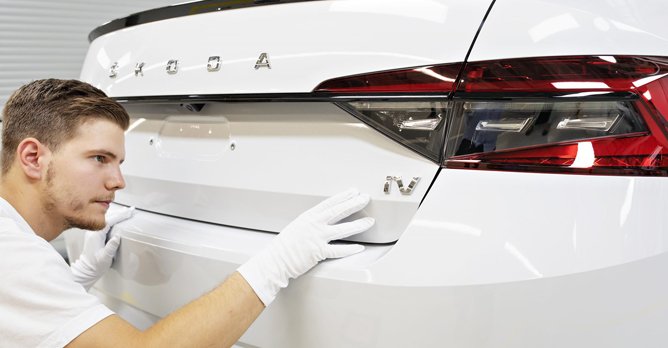

By using more Industry 4.0 technologies, Skoda will continue to push ahead with optimising the plant's production and logistics processes.
A 'BinPicking System' was introduced in mid-2019, for example, and makes use of a 3D camera system to automatically take parts required in the body shop from a container and place them on the conveyor.
The new system utilises forty new touchscreens for employees to record data, such as the length of stoppages. As a result, four times more data has been captured than with the previous system, meaning that specifics can now be analysed much more easily and comprehensively. The database now not only logs details but also stores vital information on production equipment.
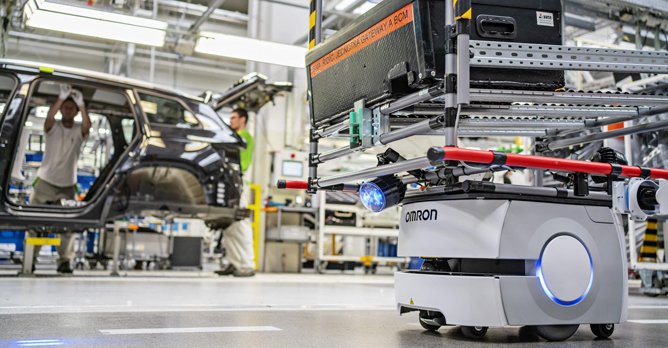

Every day, it supplies the assembly lines for the Superb, Superb iV and Kodiaq models with 2,000 parts for 400 vehicles and, unlike previous floor conveyor systems, does not require any induction loops, magnetic strips or reflection points for navigation.
To increase efficiency in warehouse logistics even further, 2020 will also see Skoda invest over $600,000 into robots that can pick starter batteries.
The Kvasiny site is also the car manufacturer's first location to utilise technology to prevent collisions between forklift trucks and employees, contributing to increasing workplace safety. The system requires staff to wear special watches that communicate with a control unit installed in the forklift trucks. These watches then draw attention to an impending collision by vibrating in a clearly perceptible manner, providing their operators with an additional warning against potential accidents.
Skoda Auto has set a new record at the Kvasiny plant by building more than 320,000 vehicles at the site in 2019.
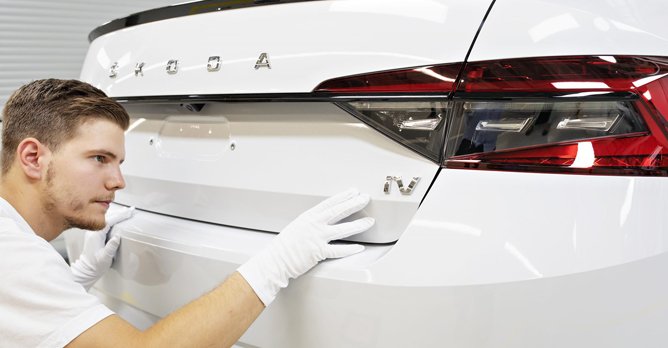

By using more Industry 4.0 technologies, Skoda will continue to push ahead with optimising the plant's production and logistics processes.
A 'BinPicking System' was introduced in mid-2019, for example, and makes use of a 3D camera system to automatically take parts required in the body shop from a container and place them on the conveyor.
The new system utilises forty new touchscreens for employees to record data, such as the length of stoppages. As a result, four times more data has been captured than with the previous system, meaning that specifics can now be analysed much more easily and comprehensively. The database now not only logs details but also stores vital information on production equipment.
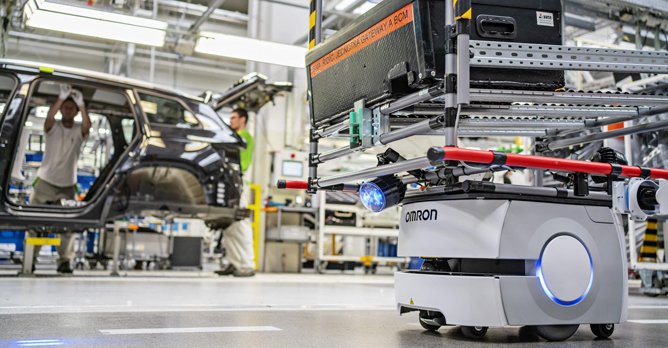

Every day, it supplies the assembly lines for the Superb, Superb iV and Kodiaq models with 2,000 parts for 400 vehicles and, unlike previous floor conveyor systems, does not require any induction loops, magnetic strips or reflection points for navigation.
To increase efficiency in warehouse logistics even further, 2020 will also see Skoda invest over $600,000 into robots that can pick starter batteries.
The Kvasiny site is also the car manufacturer's first location to utilise technology to prevent collisions between forklift trucks and employees, contributing to increasing workplace safety. The system requires staff to wear special watches that communicate with a control unit installed in the forklift trucks. These watches then draw attention to an impending collision by vibrating in a clearly perceptible manner, providing their operators with an additional warning against potential accidents.
Latest COE Prices
June 2025 | 2nd BIDDING
NEXT TENDER: 09 Jul 2025
CAT A$98,124
CAT B$116,670
CAT C$65,000
CAT E$116,889
View Full Results Thank You For Your Subscription.