Volkswagen's FSI, TSI, BlueMotion Review
19 Sep 2008|22,682 views
We've realized that rather than leave you haggling in the dark, we'll give you a short, non-exhaustive rundown on what has been shoehorned into the chassis of Volkswagens, just around the turn of the century.
Volkswagen has always claimed that in addition to high quality, reliability, safety and ecological demands, reducing fuel consumption and emissions is a significant development priority. The company has implemented its principle of combining direct injection with a spark-ignition engine in the following technologies listed below.
TDI
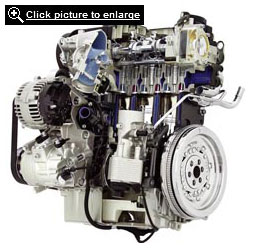
The transverse-flow cylinder head has two tangential intake ports per cylinder and a "rotated valve star". This is the term for the special arrangement of the four valves in relation to the crankshaft, which results the most favourable port geometry possible complete with an optimum combination of swirl and cylinder fill.
A crucial role in delivering optimum exhaust emissions (Euro-4) is performed by the centrally positioned 6-hole nozzle with tapered, flow-optimised injection holes. To reduce nitrogen oxides, Volkswagen uses an exhaust gas recirculation cooler, which is of a switchable design with regard to the optimum response of the two-way oxidation catalytic converter. An electric throttle valve helps in calculating exactly the exhaust gas recirculation quantity.
In addition, a new generation of unit injection elements has been developed for the four-valve engine. They are characterised by a more compact design, moderately increased partial load injection pressure and measures for effectively reducing injection noise. Volkswagen claims an 8% lower consumption compared to that of a two-valve engine that generates a comparable amount of power.
Another innovative feature typical to Volkswagen TDIs would be the diesel quick-start system with a temperature-controlled metal sheathed-element glow plug. It ensures under virtually all climatic conditions that the engine starts immediately without a long preheating phase.
And how about BlueMotion?
This is Volkswagen's environment-conscious initiative. "Blue" suggests the elements of water and air. "Motion" embodies the aspect of mobility that is looking forward into the future. Their objective is to advance BlueMotion to be the bearer of a quality seal that stands for economy without compromising driving fun.
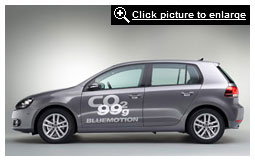
Less apparent is the thoroughly trimmed, and thereby flow-optimized underbody, as well as the nearly enclosed radiator grille. The TDI engine still gets enough cooling air by means of an effective dual fan. Even the chassis is lowered, further improving the drag coefficient value of 0.32 to 0.30.
Special 195/65 R15-sized tyres are then fitted to optimize low rolling resistance, and are driven at a higher air pressure of up to 0.3 bar more.
|
![]() |
FSI
First introduced with the Mark 4 Golf, the FSI engine delivers fuel via a common-rail system, injected directly into the combustion chamber by an electromagnetic injector at pressures of up to 100 bar. This permits precise determination of the fuel injection intervals during the cylinder working cycle and the time required for the fuel to mix with the air.
The use of direct injection makes it possible to employ the so-called stratified charge principle. In this engine operating mode, fuel is injected very shortly before ignition and, due to the specific combustion chamber geometry and a defined internal cylinder flow, is concentrated below the spark plug, so that a combustible mixture only forms at that point.
The direct injection principle developed by Volkswagen represents substantial ecological progress. Thanks to the FSI's entirely new exhaust gas after-treatment system, with fully electronic monitoring by on-board diagnosis, all pollutant substances will be converted into harmless gases.
There is a pre-converter for emission control directly after starting the engine, a three-way catalytic converter and an innovative NOx storage catalyst for converting emissions of oxides of nitrogen in the presence of excess air. The world's first integrated NOx sensor monitors the FSI engine's exhaust gas quality online. The carefully planned flow path enables the engine to operate with high excess air without mixture burn problems occurring - this is the secret of the substantially reduced fuel consumption.
An advantage of the FSI engine, as compared to other technical alternatives for minimizing fuel consumption, is that it possesses a great deal off development potential, hence Volkswagen's newest series of TSI, forced induction engines.
TSI and the Golf GT recipe
Therefore it was only natural for Volkswagen's new range of TSI engines, which only came about into the picture about 2 years ago, to be based on the current range of FSI engines.
The most effective means for reducing fuel consumption is so-called "downsizing". By reducing displacement and thereby lowering frictional losses, a lower specific fuel consumption can be achieved. This goes hand in hand with better efficiency. The innovative path to the future is the combination of supercharger and turbocharger.
The supercharger compensates for typical drive-off weakness at low revs of purely turbocharged gasoline engines, while the turbocharger really puts out at higher revs. This combination of two types of chargers is unique among engines mass-produced worldwide.
A four-valve, four-cylinder 1,390 cc engine with a cylinder pitch of 82 millimeters and a bore/stroke ratio of 76.5 to 75.6 millimeters was used in this application. In developing the TSI design efforts focused on coming up with a new cylinder crankcase of gray cast iron able to withstand severe workloads and master the 130 bar of pressure over the long term. Moreover, from a design standpoint the layout of the charger subassemblies and supercharger drive were central to the development.
|
![]() |
Modified injection technology
For the first time, the TSI engines utilize a multi-hole high-pressure injector with six fuel injection holes. As in natural aspirating FSI engines, the injector is located on the inlet side between the intake port and the level of the cylinder head gasket. In regulating flow to the injectors, the amount of fuel to be injected must be varied over a wide range in order to cover the speed range from idle to high revving at maximum power output. To cover this wide range of flow rates the maximum injection pressure was raised to 150 bar. The high compression ratio of 10:1 needed for charged engines was only possible with FSI.
A supercharger generates more torque low down in the rev range
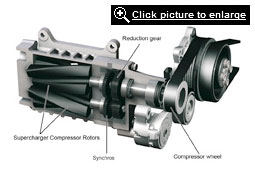
Turbocharger kicks in at the top end
At higher engine speeds the exhaust gas driven turbocharger (with wastegate control) also kicks in. The supercharger and turbo-charger are connected in series. The supercharger is actuated by a magnetic clutch that is integrated in a module within the water pump. A control door ensures that the fresh air requirements for the operating point are met in supplying the turbocharger or supercharger. In pure turbocharger operation the control door is open. The air then takes the familiar path of conventional turbocharged engines via the front air cooler and throttle valve to the induction pipe.
One of the greatest challenges in development was to determine the best possible configuration of interactions between these two chargers that are arranged in series. That is because the powertrain only achieves a uniform torque curve if the supercharger and exhaust gas turbocharger complement one another optimally. And indeed over a very wide range of engine speeds and with efficiency gains never achieved before.
|
![]() |
The maximum charge pressure of the twin charger is approx. 2.5 bar at 1,500 rpm. The supercharger is only needed to generate the required boost pressure in the speed range up to 2,400 rpm. The exhaust gas turbocharger is designed to provide an optimal level of efficiency at the upper end of performance and to provide sufficient boost pressure in the middle speed range. However the turbocharger alone is insufficient to achieve prescribed elasticity objectives during dynamic driving in the lower rpm range.
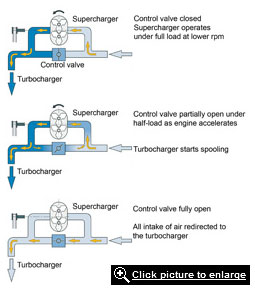
Single-charged, turbo-only TSI engine
Volkswagen then presented its new 122 bhp TSI petrol engine at the International Vienna Engine Symposium early this year, along with the world's first seven-speed dual clutch (DSG) for compact and mid-sized cars like the Golf.
Technically, the new TSI is based on its twin-charged compressor counterparts. The goal was to ensure minimum consumption by combining direct injection and turbo-charging (without the supercharger) with reduced engine capacity, thereby adding a third TSI engine to the lineup. This is in addition to the 1.8-litre turbo found in the Passat TSI.
Designed to replace the outgoing 1.6-FSI, the 1.4-litre turbo displaces 200 Nm of torque at 1,500 rpm, 30 percent higher than that of the 1.6-litre FSI, with a full 66 percent gain below 3000rpm.
In spite of the improved performance and torque characteristics, consumption has been reduced by approximately six percent.
And a little on the 7-Speed DSG
A further innovation is the seven-speed DSG. In contrast to the six-speeder, the clutches of the new gearbox do not run in an oil bath, requiring half as much engine oil to be used, further improving efficiency.
The new seven-speed DSG will soon be available for vehicles from the Polo to the Passat. The transferable maximum torque is equivalent to a maximum of 250 Nm
In the Golf, it has a fuel consumption of just 5.9 l/100 km. Both the seven-speed DSG and the 122 bhp TSI show once again that Volkswagen makes highly innovative technology available to all drivers.
|
We've realized that rather than leave you haggling in the dark, we'll give you a short, non-exhaustive rundown on what has been shoehorned into the chassis of Volkswagens, just around the turn of the century.
Volkswagen has always claimed that in addition to high quality, reliability, safety and ecological demands, reducing fuel consumption and emissions is a significant development priority. The company has implemented its principle of combining direct injection with a spark-ignition engine in the following technologies listed below.
TDI
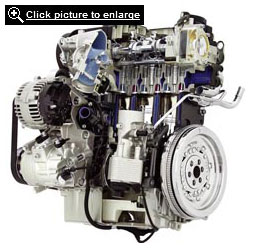
The transverse-flow cylinder head has two tangential intake ports per cylinder and a "rotated valve star". This is the term for the special arrangement of the four valves in relation to the crankshaft, which results the most favourable port geometry possible complete with an optimum combination of swirl and cylinder fill.
A crucial role in delivering optimum exhaust emissions (Euro-4) is performed by the centrally positioned 6-hole nozzle with tapered, flow-optimised injection holes. To reduce nitrogen oxides, Volkswagen uses an exhaust gas recirculation cooler, which is of a switchable design with regard to the optimum response of the two-way oxidation catalytic converter. An electric throttle valve helps in calculating exactly the exhaust gas recirculation quantity.
In addition, a new generation of unit injection elements has been developed for the four-valve engine. They are characterised by a more compact design, moderately increased partial load injection pressure and measures for effectively reducing injection noise. Volkswagen claims an 8% lower consumption compared to that of a two-valve engine that generates a comparable amount of power.
Another innovative feature typical to Volkswagen TDIs would be the diesel quick-start system with a temperature-controlled metal sheathed-element glow plug. It ensures under virtually all climatic conditions that the engine starts immediately without a long preheating phase.
And how about BlueMotion?
This is Volkswagen's environment-conscious initiative. "Blue" suggests the elements of water and air. "Motion" embodies the aspect of mobility that is looking forward into the future. Their objective is to advance BlueMotion to be the bearer of a quality seal that stands for economy without compromising driving fun.
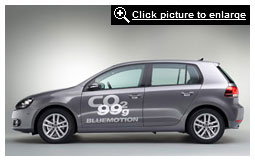
Less apparent is the thoroughly trimmed, and thereby flow-optimized underbody, as well as the nearly enclosed radiator grille. The TDI engine still gets enough cooling air by means of an effective dual fan. Even the chassis is lowered, further improving the drag coefficient value of 0.32 to 0.30.
Special 195/65 R15-sized tyres are then fitted to optimize low rolling resistance, and are driven at a higher air pressure of up to 0.3 bar more.
|
![]() |
FSI
First introduced with the Mark 4 Golf, the FSI engine delivers fuel via a common-rail system, injected directly into the combustion chamber by an electromagnetic injector at pressures of up to 100 bar. This permits precise determination of the fuel injection intervals during the cylinder working cycle and the time required for the fuel to mix with the air.
The use of direct injection makes it possible to employ the so-called stratified charge principle. In this engine operating mode, fuel is injected very shortly before ignition and, due to the specific combustion chamber geometry and a defined internal cylinder flow, is concentrated below the spark plug, so that a combustible mixture only forms at that point.
The direct injection principle developed by Volkswagen represents substantial ecological progress. Thanks to the FSI's entirely new exhaust gas after-treatment system, with fully electronic monitoring by on-board diagnosis, all pollutant substances will be converted into harmless gases.
There is a pre-converter for emission control directly after starting the engine, a three-way catalytic converter and an innovative NOx storage catalyst for converting emissions of oxides of nitrogen in the presence of excess air. The world's first integrated NOx sensor monitors the FSI engine's exhaust gas quality online. The carefully planned flow path enables the engine to operate with high excess air without mixture burn problems occurring - this is the secret of the substantially reduced fuel consumption.
An advantage of the FSI engine, as compared to other technical alternatives for minimizing fuel consumption, is that it possesses a great deal off development potential, hence Volkswagen's newest series of TSI, forced induction engines.
TSI and the Golf GT recipe
Therefore it was only natural for Volkswagen's new range of TSI engines, which only came about into the picture about 2 years ago, to be based on the current range of FSI engines.
The most effective means for reducing fuel consumption is so-called "downsizing". By reducing displacement and thereby lowering frictional losses, a lower specific fuel consumption can be achieved. This goes hand in hand with better efficiency. The innovative path to the future is the combination of supercharger and turbocharger.
The supercharger compensates for typical drive-off weakness at low revs of purely turbocharged gasoline engines, while the turbocharger really puts out at higher revs. This combination of two types of chargers is unique among engines mass-produced worldwide.
A four-valve, four-cylinder 1,390 cc engine with a cylinder pitch of 82 millimeters and a bore/stroke ratio of 76.5 to 75.6 millimeters was used in this application. In developing the TSI design efforts focused on coming up with a new cylinder crankcase of gray cast iron able to withstand severe workloads and master the 130 bar of pressure over the long term. Moreover, from a design standpoint the layout of the charger subassemblies and supercharger drive were central to the development.
|
![]() |
Modified injection technology
For the first time, the TSI engines utilize a multi-hole high-pressure injector with six fuel injection holes. As in natural aspirating FSI engines, the injector is located on the inlet side between the intake port and the level of the cylinder head gasket. In regulating flow to the injectors, the amount of fuel to be injected must be varied over a wide range in order to cover the speed range from idle to high revving at maximum power output. To cover this wide range of flow rates the maximum injection pressure was raised to 150 bar. The high compression ratio of 10:1 needed for charged engines was only possible with FSI.
A supercharger generates more torque low down in the rev range
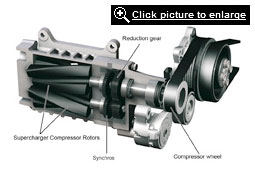
Turbocharger kicks in at the top end
At higher engine speeds the exhaust gas driven turbocharger (with wastegate control) also kicks in. The supercharger and turbo-charger are connected in series. The supercharger is actuated by a magnetic clutch that is integrated in a module within the water pump. A control door ensures that the fresh air requirements for the operating point are met in supplying the turbocharger or supercharger. In pure turbocharger operation the control door is open. The air then takes the familiar path of conventional turbocharged engines via the front air cooler and throttle valve to the induction pipe.
One of the greatest challenges in development was to determine the best possible configuration of interactions between these two chargers that are arranged in series. That is because the powertrain only achieves a uniform torque curve if the supercharger and exhaust gas turbocharger complement one another optimally. And indeed over a very wide range of engine speeds and with efficiency gains never achieved before.
|
![]() |
The maximum charge pressure of the twin charger is approx. 2.5 bar at 1,500 rpm. The supercharger is only needed to generate the required boost pressure in the speed range up to 2,400 rpm. The exhaust gas turbocharger is designed to provide an optimal level of efficiency at the upper end of performance and to provide sufficient boost pressure in the middle speed range. However the turbocharger alone is insufficient to achieve prescribed elasticity objectives during dynamic driving in the lower rpm range.
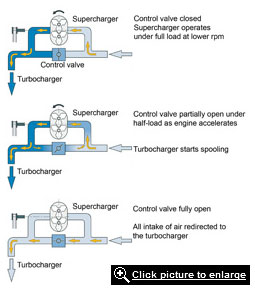
Single-charged, turbo-only TSI engine
Volkswagen then presented its new 122 bhp TSI petrol engine at the International Vienna Engine Symposium early this year, along with the world's first seven-speed dual clutch (DSG) for compact and mid-sized cars like the Golf.
Technically, the new TSI is based on its twin-charged compressor counterparts. The goal was to ensure minimum consumption by combining direct injection and turbo-charging (without the supercharger) with reduced engine capacity, thereby adding a third TSI engine to the lineup. This is in addition to the 1.8-litre turbo found in the Passat TSI.
Designed to replace the outgoing 1.6-FSI, the 1.4-litre turbo displaces 200 Nm of torque at 1,500 rpm, 30 percent higher than that of the 1.6-litre FSI, with a full 66 percent gain below 3000rpm.
In spite of the improved performance and torque characteristics, consumption has been reduced by approximately six percent.
And a little on the 7-Speed DSG
A further innovation is the seven-speed DSG. In contrast to the six-speeder, the clutches of the new gearbox do not run in an oil bath, requiring half as much engine oil to be used, further improving efficiency.
The new seven-speed DSG will soon be available for vehicles from the Polo to the Passat. The transferable maximum torque is equivalent to a maximum of 250 Nm
In the Golf, it has a fuel consumption of just 5.9 l/100 km. Both the seven-speed DSG and the 122 bhp TSI show once again that Volkswagen makes highly innovative technology available to all drivers.
|
Thank You For Your Subscription.